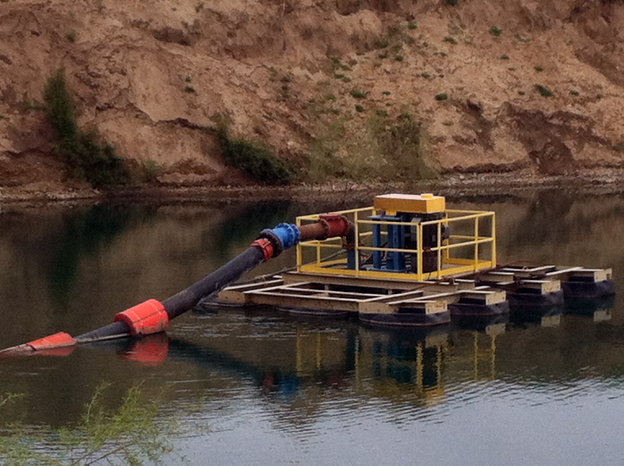
Saves more than $30,000 annually through new installation efficiency and productive increases
A large California construction company boasting more than 5000 employees had a seepage problem. As one of the top ten producers of both aggregate and sand/gravel products, the company wanted to extract aggregate from around a gravel pit that frequently filled with water, in large part because the pit sits atop an underground river.
To combat the water, the company had installed another manufacturer’s pump on barges to dewater the pit and transfer the water out of the area. However, these vertical pumps were not performing to expectations. More water than was acceptable was filling the pit—making extraction less effective, and therefore more expensive. The problem was exacerbated when the company dug for new material; they got closer to the underground river and increased the seepage rate.
The area Cornell distributor had a solution: barge-mount several pumps at 45 degree angles to maintain efficiencies and minimize suction lift. The barges and a four foot by three foot strainer basket with a solid steel top to prevent vortex were designed in concert with Cornell Pump engineering. The pumps also had to be more efficient, given the high cost of electricity in this area of California.
Two Cornell 12NHTB-F18DB pumps utilizing grease lubed bearing frames drive the new design. Cornell NHTB pumps were chosen because of their superior solids handling characteristics. Through the increased efficiencies of the pumps, the aggregate company saves more than $10,000 per pump annually, plus additional tens of thousands of dollars per year in increase production from not extracting materials under higher water conditions.